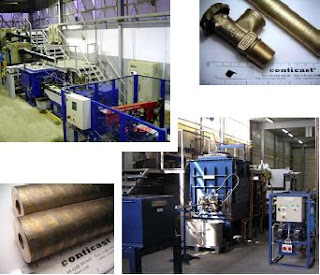
Empresa: PYPESA
Una vez verificada la aptitud del material recepcionado, se almacena separando las virutas de los recortes, rebabas y puntas de barra macizas. Se utiliza también materias primas vírgenes en lingote para refinar las aleaciones que se pretenden fabricar.
Un primer horno fusor y un posterior horno de mantenimiento completan el ciclo consiguiendo con ello una homogeneidad en la aleación obtenida, un afino de grano y unos parámetros de sus componentes, acordes con el requerimiento de cada fabricación. Interviene también en este proceso el Departamento de Calidad, que analiza varias probetas en cada colada efectuando análisis por espectrometría, antes de verter el caldo a la máquina de colar, donde se obtiene el TOCHO o BILLET.
Una vez colado el tocho, en su longitud y estado original, se enfría, se corta y se almacena según su composición (aleación), diámetro y longitud. El análisis de cada colada correspondiente figurará en el certificado de calidad final de cada lote fabricado y persiguiendo desde principio hasta la obtención final del fardo de barras o palet de rollos, donde en la etiqueta figurará el número de fabricación y de colada, garantizando la correcta trazabilidad de todo el proceso.
Existen algunas fábricas que eliminan este proceso y suministran barras directas de colada utilizando coquillas o bocas de distintos diámetros. Estas barras se repelan a posteriori por torneado y se consiguen calidades en algunos casos aceptables para determinadas utilizaciones con pocos requerimientos de calidad. Pueden tener problemas de comportamiento sobre todo en el mecanizado, no siendo aconsejable su utilización en CNC por el tamaño y distribución de grano, también no es recomendable su uso en la fabricación de piezas para gas (llaves, válvulas racores, etc.) ante la posibilidad de que aparezcan fugas por poros en las barras. En la fabricación de la barra extrusionada, esto no ocurre, completando el ciclo con los siguientes procesos.
Calentamiento de los TOCHOS.
Extrusión.
Que elimina la capa de óxido inherenteal proceso de extrusión en caliente. Calibrado, enderezado, pulido, apuntado y biselado de extremos. En este proceso se incluye también la eliminación y saneamiento de las puntas del material extrusionado, y se verifica también la longitud de las barras, rectitud y diámetro, asegurando que esté dentro de tolerancias.
En los casos que se requiera, se trata térmicamente la barra, sometiéndola a recocido, estabilizado o distensionado.